Why Machine Safety Is Important & How Thyristors Can Help
Why is machine safety important? At its core, it’s about protecting lives and maintaining smooth operations. Without proper safety measures, the risk of accidents skyrockets, and productivity can plummet. In the paragraphs that follow, we explore the imperative nature of machine safety, its impact on people and performance, and the technical solutions like thyristors that can help uphold these essential standards.
Key Takeaways
- Machine safety is crucial for preventing injuries and fatalities, boosting employee morale, and fulfilling legal and ethical obligations.
- Thyristor (SCR) Power Controllers enhance machinery safety by controlling power surges and overheating, offering stable power levels for consistent power control.
- A comprehensive safety approach involves risk assessments, implementation of safety devices, regular maintenance, and employee training to create a culture of safety within the workplace.
Understanding the Significance of Machine Safety
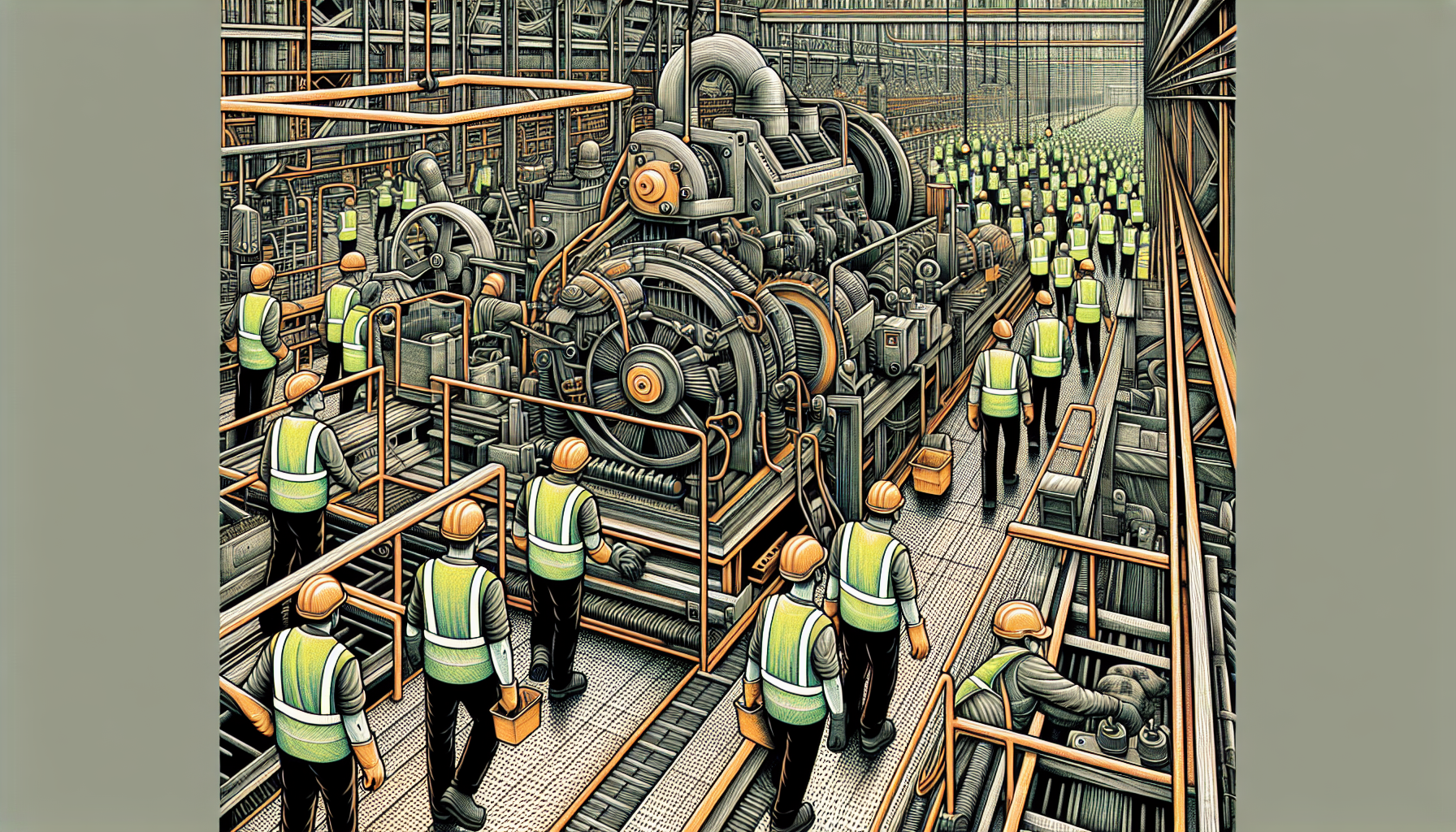
who interact with machines. Imagine a workplace where machines operate efficiently without interference, where downtime is reduced, and productivity is enhanced. That’s the magic of implementing proper safety measures.
But beyond the financial implications, it also fosters a safer working environment, boosting employee morale. After all, safety is not just about preventing accidents; it’s about creating a culture of care.
The Human Cost: Injuries and Fatalities
Juxtaposed with the benefits of machine safety is the grim reality of what happens when it’s neglected. On average, 22 workers per year lose their lives due to contact with machinery in manufacturing industries. A significant percentage of non-fatal injuries are also attributed to machinery contact. These stark figures underscore the critical importance of effective machine safety measures.
Remember, every life saved is a family preserved, a dream nurtured, a future secured.
Legal and Ethical Obligations
The commitment to machine safety extends beyond the walls of the workplace. Employers are legally bound to ensure machinery is safe, well-maintained, and carries the CE mark. Adherence to machine safety standards isn’t just a legal requirement; it’s an ethical obligation.
Because when it comes to safety, the question isn’t “Can we afford to?” but “Can we afford not to?”
The Role of Thyristors in Enhancing Machinery Safety
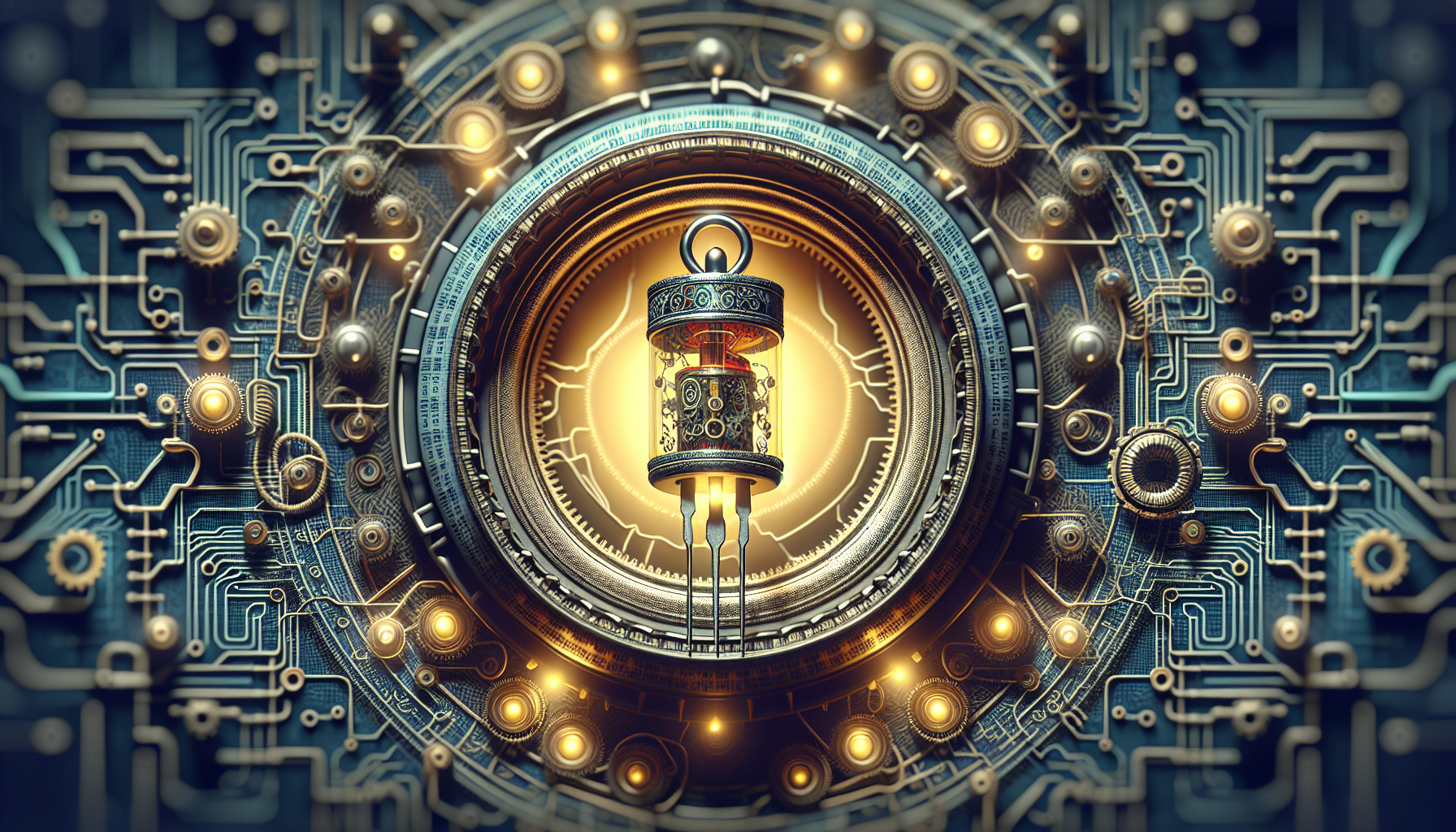
Now, you might wonder, where do thyristors fit into this picture? Thyristors act as robust switches managing high-power applications like:
- motor speed control
- power factor correction
- voltage regulation
- current limiting
Their role in ensuring stable power levels helps prevent equipment failures or production inconsistencies, contributing to machinery safety.
In other words, thyristors provide a blanket of security that shields both staff and machinery from power problems such as overheating and power surges.
Basics of Thyristor Technology
Before we delve deeper into how thyristors enhance safety, let’s understand what they are. Thyristors are semiconductor devices that function as bi-stable switches controlled by a gate electrode. They regulate power by adjusting voltage and current waveforms, offering smooth control and avoiding the wear and tear common with traditional switches.
This reliable and efficient control of power is a crucial element in the safe operation of machinery.
Preventing Power Surges and Overheating
Thyristors don’t just regulate power; they serve as vigilant guardians, preventing power surges and overheating. Imagine the chaos that a sudden power spike could cause in a manufacturing plant. To mitigate this, thyristors feature rapid response times for real-time adjustments, preventing voltage surges and safety hazards like fires or electrical shocks.
In terms of overheating, thyristors are designed with larger circuit board tracking, junctions, and semi-conductors, ensuring component reliability and longevity.
Consistent Power Control with Microprocessors
Microprocessor-based controllers are the unsung heroes of machinery safety. They use thyristors with control to maintain consistent power output, preventing element stress and failure. This feature is particularly handy when the element resistance varies over time, ensuring that the power output remains consistent.
Thyristors also have a ‘heater break alarm’ feature to inform operators when an element has broken, further preventing element stress and ultimately failure.
Implementing Proper Safety Measures: A Multi-Faceted Approach
Building a fortress of safety around machines is no mean feat. It requires a comprehensive approach that includes risk assessment, protective measures such as safety devices, and employee training. Machines should be fitted with fixed or adjustable guards to prevent access to dangerous parts. Safety devices, such as emergency stop buttons, should be within easy reach.
But safety measures aren’t just about equipment. It’s also about arming employees with knowledge through training programs and occupational safety information.
Risk Assessment: Identifying Potential Hazards
Risk assessment is the compass that guides safety measures. It involves identifying potential hazards and evaluating their risks. This evaluation is essential not just for implementing safety measures but also for obtaining the CE marking necessary for marketing within the European Economic Area. In this process, the health and safety executive plays a crucial role in ensuring compliance with regulations.
Risk reduction should prioritise inherently safe design and include technical safety features like emergency shutdowns. If hazards remain, operators should be informed about residual risks to enhance safety measures.
Safety Equipment and Devices
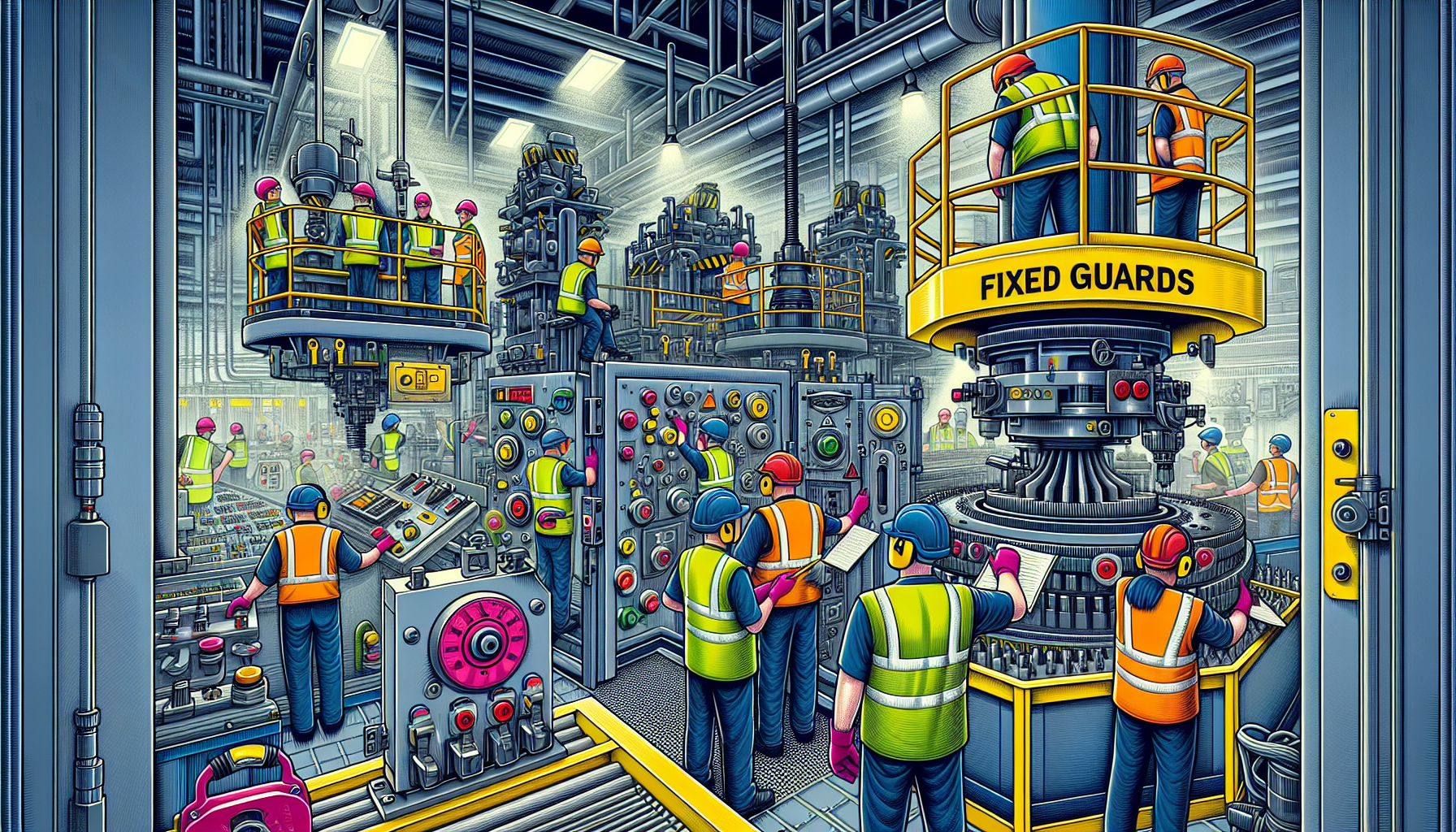
Safety equipment and devices are the shields in our quest for machinery safety. Essential machinery safety measures include:
Furthermore, Personal Protective Equipment (PPE), which includes appropriate safety equipment, is crucial to protect users from potential injuries when working with machinery.
These safety measures, paired with regular maintenance and upgrades, ensure that the equipment continues to serve its purpose effectively.
Training and Awareness
Knowledge is power, and nowhere is this truer than machine safety. Proper training for machine operators encompasses the necessary skills, knowledge, and potentially formal qualifications to ensure the safe use of machinery. Supervisors, too, must receive specific training to oversee machinery effectively.
Regular safety meetings and training sessions, led by a safety executive, are crucial in updating employees about safety procedures and allow them to share safety-related experiences, reinforcing a safety-conscious work environment.
Advances in Machine Guarding: From Fixed Guards to Sophisticated Systems
Machine guarding has come a long way from rudimentary fixed guards. Today, it incorporates smart sensors and automation for real-time monitoring and immediate adjustments to prevent accidents. These sophisticated systems are flexible and modular, adaptable to different machines, and improve the ease of maintenance and installation.
Traditional Guarding Solutions
Despite the advent of new technologies, traditional guarding solutions retain their fundamental role in ensuring safety. Some examples of conventional guarding solutions include:
- Fixed guards
- Interlocked guards
- Adjustable guards
- Self-adjusting guards
- Other devices
These guards and devices play a central part in the safeguarding of machinery. They are designed to eliminate the possibility of introducing new hazards, such as creating sharp edges or points that could harm workers.
Their robust and tamper-resistant construction ensures their continued effectiveness in fulfilling their safety role.
Smart Safety Devices
Smart safety devices represent a significant stride in machine safety. Motion detection sensors, designed to interface seamlessly with machinery controls, promptly identify erratic movements in machinery parts and can halt operations to prevent potential accidents.
Proximity sensors equipped with infrared or ultrasonic technology detect when operators or objects are in close vicinity to machines, initiating an automatic shutdown or slowdown to avoid accidents. Pressure-sensitive mats can also be used as an additional safety measure in such scenarios.
Importance of Regular Maintenance and Upgrades
Regular maintenance and upgrades are the lifeblood of machinery safety. A proactive maintenance program ensures the safety of both the maintenance crew and machine operators by adhering to the manufacturer’s advice and best engineering practices.
Machine guards should be designed to allow for essential maintenance like lubrication without the need to remove the guard, thereby maintaining protection during maintenance activities.
Creating a Culture of Safety in the Workplace
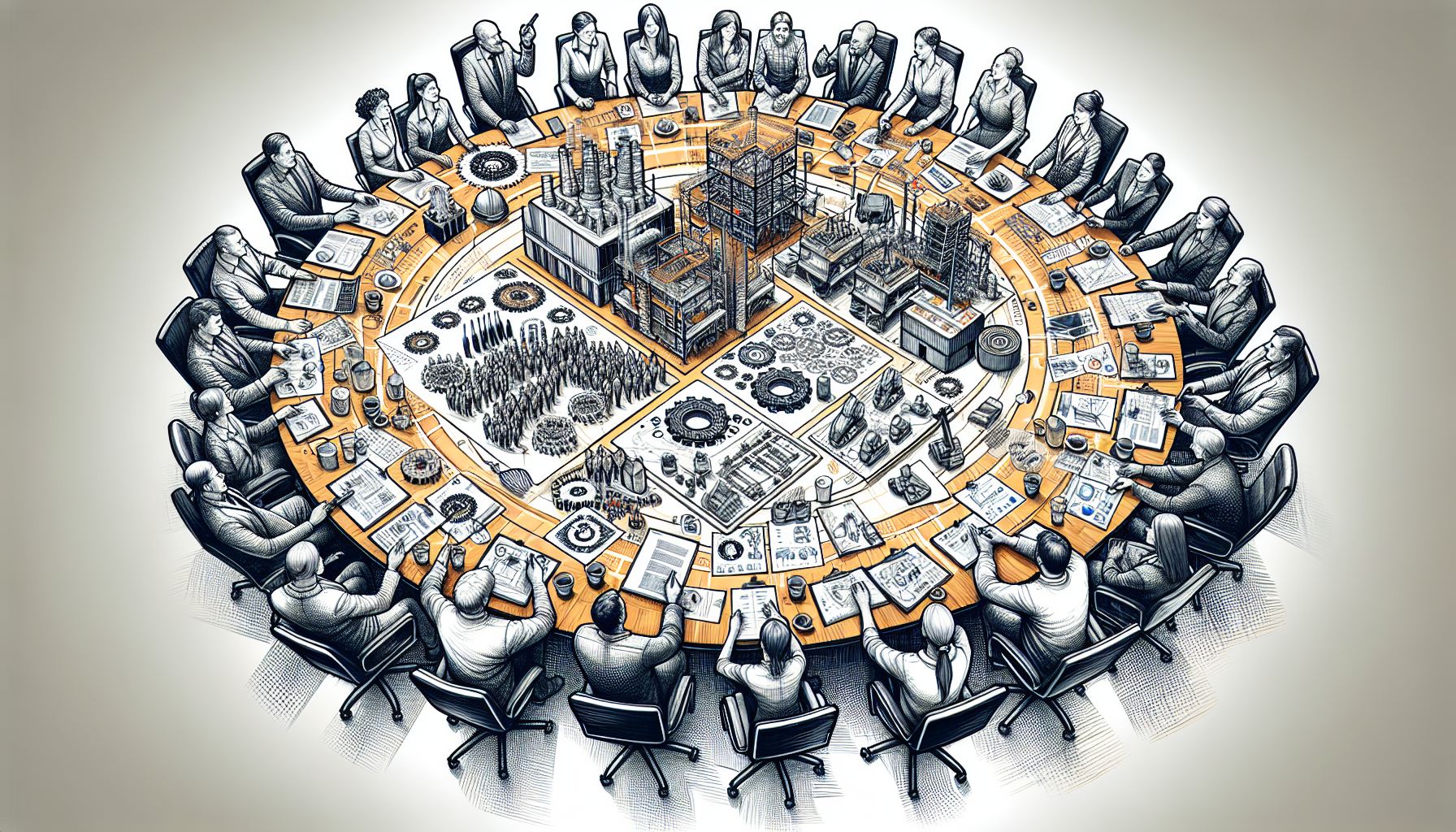
Fostering a culture of safety in the workplace is not a one-time event; it’s an ongoing process. It takes leadership commitment, clear guidelines, and active employee involvement. Leaders set the tone for safety, with managers setting a precedent and remaining approachable to the workforce.
But cultivating a safety culture goes beyond policies and equipment; it’s about embedding safety in the very fabric of the organisation’s culture.
Clear Guidelines and Communication
Clear guidelines and effective communication are the backbone of a safety culture. Workers should be informed about the company’s safety policy and how it translates into practical measures. Regular safety meetings and bulletins maintain clear guidelines and effective communication about workplace safety.
Having a safety newsletter or blog can keep employees informed and engaged, further fostering a safety-conscious work environment to protect workers.
Encouraging Employee Involvement
Involving employees in safety initiatives is just as crucial as setting clear guidelines. Establishing channels where employees can report safety concerns and offer suggestions without fear of retaliation promotes open communication and trust.
Recognising and rewarding adherence to safety procedures can motivate employees’ continued commitment to safety initiatives. After all, safety is everyone’s responsibility.
Addressing Mechanical Hazards: Specific Examples and Solutions
Machines, while impressive feats of engineering, can present a myriad of mechanical hazards. These can range from being struck by moving parts and getting entangled in machinery, to coming in contact with hot or cold parts. Addressing these hazards involves identifying specific risks, such as sharp pointed parts and heavy equipment, and implementing targeted solutions.
Dealing with Sharp-Pointed Parts
Sharply-pointed machinery parts can present significant hazards. Injuries can range from clothing, fingers, hair, or jewellery becoming entangled in machinery, which can lead to severe consequences. Managing these risks requires active prevention measures, such as securing dangerous parts or seeking alternative machinery that eliminates the need for the blade and the associated risks.
Managing Risks from Heavy Equipment
Heavy equipment can pose challenges due to remote controls, restricted visibility, and the hazard of loads affecting the centre of gravity. Mitigating these risks can involve strategic placement of warning signs and establishing zones that are excluded from equipment operation in compliance with work equipment regulations.
Advanced technologies like automated guided vehicles with sensor and navigation technology are used to transport materials within manufacturing facilities and help avoid collisions.
Summary
As we journeyed through the world of machine safety and the role of thyristors, we delved into the significance of safety measures, the importance of regular maintenance and upgrades, and the need for a safety-conscious culture in the workplace. We also explored the potential hazards that machinery can present and how these can be mitigated through strategic measures and the use of safety equipment and devices.
In the end, the ultimate goal is a safer working environment where employees can perform their tasks without fear of accidents or injuries. This goal is not an endpoint but a continuous journey. It requires constant vigilance, ongoing training, and a commitment to safety that goes beyond compliance with standards and regulations. It’s about placing human well-being at the heart of everything we do because safety, after all, is not just a protocol; it’s a promise.
For more information on Thyristor (SCR) Power Controllers, get in touch with our team here at CD Automation by calling 01323 811 100 or requesting an online quote today.
Frequently Asked Questions
How do Thyristor power controllers overcome power surges on start-up?
Thyristor power controllers overcome power surges on start-up by providing functionality such as soft start, current limit, and phase angle firing, which help regulate the power.
How do microprocessor-based controllers ensure consistent power control?
Microprocessor-based controllers ensure consistent power control by using feedback control to keep the power output consistent despite variations in element resistance over time.
How do Thyristors make machinery safer?
Thyristors make machinery safer by incorporating built-in systems to reduce the risk of power issues, including overheating, power surges, and inconsistent power control. This ultimately enhances the overall safety of the machinery.
How do CD Automation power units prevent potential fire risks?
CD Automation power units prevent potential fire risks by automatically shutting down at 90°C. This feature ensures safety and minimises the risk of fire hazards.
How do Thyristors protect against high temperatures?
Thyristors are designed with larger circuit board tracking, junctions, and oversized semiconductors to protect against the negative effects of high temperatures. This design helps prevent damage from overheating.