Constant Current vs Constant Voltage: Enhancing Electrical Heating with Thyristor Power Controllers
In industrial and commercial applications, precise control of electrical heating processes is essential for maintaining efficiency, safety, and product quality. Voltage regulation is crucial in maintaining efficiency and safety in these processes. Incorporating control feedback mechanisms, especially when using thyristor power controllers as the switching device, can significantly enhance the performance of these heating systems. This article explores how control feedback and constant current regulation can improve the performance of your electrical heating process and the pivotal role of thyristor power controllers in this improvement.
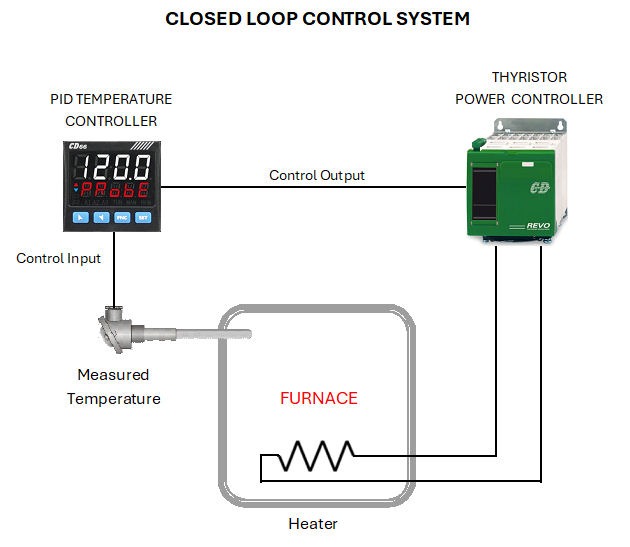
Understanding Thyristor Power Controllers
Thyristor power controllers are semiconductor devices used to regulate power flow to electrical heating elements. They are part of power supply circuits that convert incoming electricity into usable forms for heating elements, ensuring effective load regulation to handle changes in load conditions. They are favoured for their ability to handle high power current and constant voltage levels, fast switching capabilities, and precise control over power delivery. When combined with control feedback mechanisms, thyristor power controllers can achieve remarkable improvements in heating process performance.
Key Feedback Modes in Electrical Heating with Thyristor Power Controllers
Constant Current Feedback
Monitors and adjusts the current flowing to the heating elements to maintain constant voltage at the desired current level. Current limiting is used to prevent excessive current flow in constant current feedback systems, ensuring the safety and longevity of the components.
Constant current power supplies are designed to maintain a constant level of steady electric current regardless of changes in load or voltage, which is crucial for applications like battery charging.
Constant Voltage Feedback
Regulates the constant voltage power being supplied to the heating elements to ensure stability and prevent fluctuations.
Constant voltage power supplies can maintain stable voltage outputs despite changes in load conditions, which is essential for the reliable operation of electronic circuits.
Moving from the kitchen to the factory floor, temperature control continues to play a vital role. In manufacturing, precise temperature control maximizes material properties and minimizes waste. Accurate temperature regulation turns raw materials into high-quality goods through efficient production processes, leading to better financial results and customer satisfaction.
Power Feedback:
Controls the total voltage source of power delivered to the heating elements, optimising efficiency and performance. Power factor correction is used to optimise efficiency and performance in power feedback systems.
How Control Feedback Improves Heating Process Performance
Enhancing Temperature Stability
Negative Feedback: By utilising negative feedback loops, thyristor power controllers can stabilise the heating process through effective temperature control. Maintaining a stable output voltage is crucial for preventing temperature fluctuations and ensuring consistent performance in heating processes. This involves continuously monitoring the output temperature and adjusting the power delivery to maintain the output voltage and set temperature, minimising fluctuations.
Example: In a furnace, negative feedback helps maintain a consistent temperature, which is crucial for processes such as metal annealing, where a relatively constant level of uniform temperature is critical for product quality.
Improving Accuracy
Precise Control: Feedback mechanisms provide precision control over the heating elements by continuously comparing the actual temperature with the desired setpoint and making real-time adjustments. A constant voltage power supply ensures that the voltage remains stable, which is essential for accurate control of heating elements.
Example: In a plastic moulding process, precise temperature control ensures that the plastic melts uniformly, resulting in high-quality moulded parts.
Enhancing Efficiency
Optimised Power Usage: Power feedback systems adjust the power delivered to the heating elements based on the actual demand, reducing energy consumption and improving overall energy efficiency. An efficient power supply is crucial for optimising power usage and reducing energy consumption in heating processes.
Example: In industrial ovens, power feedback helps optimise energy use, leading to significant cost savings while maintaining the required heating levels.
Protecting Power Supply Equipment
Overcurrent and Overvoltage Protection: Feedback mechanisms can detect abnormal conditions in the power source, such as overcurrent or overvoltage and take corrective actions to protect the heating elements and other components. Power supply circuits are designed to prevent overcurrent and overvoltage conditions, protecting heating elements and other components. Overload protection is used to prevent overcurrent and overvoltage conditions in power supply circuits, ensuring the safety and longevity of the equipment.
Example: In a kiln used for ceramics, feedback can shut down or reduce the power supply to prevent damage to the heating elements due to overcurrent conditions.
Dynamic Response to Changes
Adaptive Control: Feedback systems enable thyristor power supplies and controllers to quickly adapt to changes in load or operating conditions, ensuring consistent performance even under varying demands. Load adaptability is crucial for ensuring consistent performance under varying demands.
Example: In a food processing plant, feedback allows the heating system to adjust rapidly to different cooking loads, maintaining consistent cooking temperatures.
Improved Safety
Preventing Overheating: Feedback mechanisms help prevent overheating, ensuring that the temperature does not exceed safe levels, thereby enhancing the safety of the heating process. Safety mechanisms are used to prevent overheating and ensure safe operation in heating processes.
Example: In chemical processing, feedback ensures that reactors do not overheat, preventing dangerous reactions and ensuring safe operation.
Applications of Control Feedback in Electrical Heating with Thyristor Power Controllers
- Industrial Furnaces: Precise temperature control for processes such as metal treatment, ceramics, and glass manufacturing.
- Plastic Molding: Uniform heating for consistent product quality in plastic moulding operations.
- Food Processing: Maintaining optimal cooking temperatures in food production lines.
- Chemical Processing: Safe and controlled heating in chemical reactors.
- HVAC Systems: Efficient and stable heating in residential and commercial heating systems.
- Industrial Automation: Control feedback plays a crucial role in optimising heating processes within industrial automation, ensuring precise temperature regulation and enhancing overall system efficiency.
Additional Considerations for Implementing Thyristor Power Controllers
Integration with Modern Technologies
IoT and Smart Systems: Modern thyristor power controllers can be integrated with IoT (Internet of Things) and smart systems to provide real-time monitoring and control. This integration allows for remote adjustments and data collection, which can be used for predictive maintenance and further optimisation of heating processes.
Energy Management
Sustainable Practices: Implementing thyristor power controllers with control feedback mechanisms can contribute to energy management and sustainability goals. By optimising power usage and reducing energy consumption, industries can lower their carbon footprint and contribute to environmental conservation.
Customisation and Scalability
Tailored Solutions: Thyristor power controllers can be customised to meet specific requirements of different applications. Whether it’s a small-scale operation or a large industrial setup, these controllers can be scaled and tailored to provide optimal performance and efficiency.
Training and Maintenance
Operator Training: Proper training for operators and maintenance personnel is essential to ensure the effective use of thyristor power controllers. Understanding the principles of control feedback and the specific features of these controllers can lead to better handling and troubleshooting.
Routine Maintenance: Regular maintenance checks and updates are crucial to keep the thyristor power controllers functioning efficiently. This includes inspecting connections, updating software, and ensuring that all components are in good working condition.
Future Trends
Advancements in Materials: Ongoing research and development in materials science may lead to the creation of more efficient and durable thyristor power controllers. This could result in even greater improvements in the performance and longevity of heating systems.
Enhanced Algorithms: The development of more sophisticated control algorithms can further enhance the precision and efficiency of feedback mechanisms in thyristor power controllers. These advancements could lead to smarter and more adaptive heating solutions.
Global Standards: As industries continue to adopt these technologies, global standards and best practices will evolve. Staying updated with these standards can ensure that implementations are in line with the latest safety and efficiency guidelines.
By considering these additional factors, industries can maximise the benefits of thyristor power controllers and control feedback mechanisms, leading to more efficient, safe, and sustainable heating processes.
Conclusion
Integrating control feedback mechanisms with thyristor power controllers in electrical heating processes can significantly enhance performance. By improving temperature stability, accuracy, efficiency, equipment protection, and safety, feedback systems ensure that heating processes operate optimally. The dynamic response capabilities of feedback mechanisms allow heating systems to adapt to changing conditions, maintaining consistent and reliable performance. For any industrial or commercial application requiring precise and efficient heating, incorporating control feedback with thyristor power controllers is a powerful strategy to achieve superior results.