Demonstrating Integrity: The Importance of Proving Your Product Meets its Manufactured Specification & Process
In today’s manufacturing landscape, especially within industries relying on precision and durability, proving that a product meets its specified manufacturing process and standards is vital. This is particularly true in sectors where electrical heating processes and heat treatment play a critical role in ensuring product quality. Demonstrating that these processes are correctly implemented not only underscores product integrity but also builds trust with customers, regulatory bodies, and stakeholders. This article explores the significance of approvals, product manufacturing traceability, adherence to regulations, and compliance with both UK and international standards, with a special emphasis on the critical roles of electrical heating and heat treatment in manufacturing.
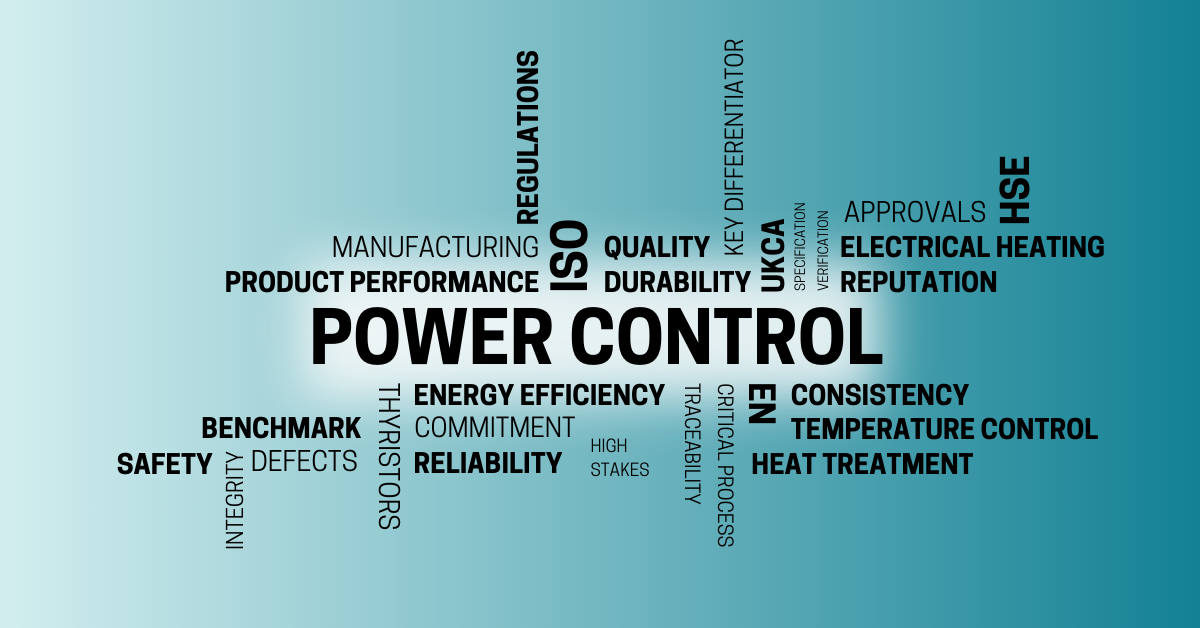
Approvals: Building Confidence Through Verification
Obtaining approvals is a fundamental step in proving that a product has been manufactured according to its specified processes, particularly when these processes involve critical steps like electrical heating and heat treatment. In the UK, approvals from regulatory bodies such as the British Standards Institution (BSI), industry associations, or third-party certifiers provide formal endorsements that a product complies with established safety, performance, and environmental standards.
These approvals are crucial for several reasons. They give manufacturers assurance that their products meet legal and industry requirements, essential for avoiding penalties, recalls, or bans on non-compliant products. Additionally, approvals are often necessary to access key markets, particularly in regions with stringent regulatory environments, such as the UK, the European Union, and North America.
For customers and end-users, approvals act as a trusted signal that the product has undergone rigorous testing and meets recognized standards. This is especially important for products involving electrical heating and heat treatment, where precise temperature control and process consistency are critical to ensuring product safety, performance, and durability.
Product Manufacturing Traceability: Ensuring Accountability and Quality
Proving that a product meets its manufacturing specifications, especially when it involves heat treatment processes, requires robust traceability throughout the production cycle. Traceability involves documenting every stage of production, which allows manufacturers to track the history, application, or location of a product or its components.
Traceability is vital in heat treatment processes, where maintaining specific temperatures and exposure times can drastically impact the material properties of the final product. By keeping detailed records of each step, including temperature profiles and heating durations, manufacturers can quickly identify and address any deviations from the specified process. This capability not only improves product quality but also reduces the risk of costly defects or recalls.
Moreover, traceability supports accountability. In industries where heat treatment is critical—such as in aerospace, automotive, and tool manufacturing—having a clear record of the production history, including all heat treatment processes, is crucial for legal and regulatory purposes. This transparency ensures that the product was produced according to the highest standards and reinforces the manufacturer’s commitment to quality and safety.
Regulations: The Framework for Compliance and Integrity
Adhering to regulations is essential in proving that a product meets its manufactured specifications, particularly in processes involving electrical heating and heat treatment. In the UK, regulations provided by bodies such as the Health and Safety Executive (HSE) and standards associated with the UK Conformity Assessed (UKCA) marking system govern how these processes should be conducted.
These regulations provide the legal framework for ensuring that products are safe, reliable, and produced under controlled conditions. For instance, regulations around electrical heating processes might specify requirements for energy efficiency, safety features to prevent overheating, and protocols for monitoring and maintaining precise temperature control. Similarly, heat treatment processes must adhere to strict standards to ensure that materials achieve the required mechanical properties without compromising safety or integrity.
Failure to comply with these regulations can lead to severe consequences, including financial penalties, legal action, and reputational damage. For manufacturers, especially those involved in high-stakes industries like aerospace or automotive, staying informed about these regulatory requirements and ensuring compliance is not just a legal obligation but also a crucial aspect of maintaining product integrity.
Standards: Ensuring Consistency and Reliability
Standards are the benchmarks that define the specifications and processes for manufacturing products, and they are particularly critical when it comes to electrical heating and heat treatment processes. In the UK, these standards include British Standards (BS), as well as international guidelines set by organizations like the International Organization for Standardization (ISO) and European Standards (EN).
Adhering to these standards is crucial for proving that a product meets its manufacturing specifications. Standards ensure consistency and reliability, particularly important in heat treatment processes where even slight deviations in temperature or time can lead to significant differences in product performance. By following established standards, manufacturers can ensure that their products exhibit the desired physical and mechanical properties, such as hardness, strength, and resistance to wear.
Standards also provide clear guidelines that help streamline the production process, reducing the likelihood of errors and defects. This not only enhances product quality but also demonstrates the manufacturer’s commitment to meeting or exceeding industry norms. In processes involving electrical heating and heat treatment, adherence to standards is often a key differentiator that assures customers of the product’s quality and durability.
Conclusion
In conclusion, demonstrating that a product meets its manufactured specifications and process is essential for maintaining integrity in the UK manufacturing industry, especially in sectors involving electrical heating and heat treatment. Approvals, traceability, regulations, and standards all play a crucial role in this process. By ensuring that these critical processes are properly managed and documented, manufacturers can build trust with customers, avoid legal and financial risks, and contribute to the overall quality and safety of the products they bring to market. This commitment to integrity is what ultimately distinguishes leading manufacturers in today’s competitive environment, both in the UK and globally.