Understanding Variable Resistance Heating Elements: Silicon Carbide, Molybdenum Disilicide, and Nichrome
In the world of industrial heating, precision and efficiency are paramount. Whether it’s in the production of glass, the processing of metals, or the creation of advanced ceramics, the ability to control temperature accurately can significantly impact the quality of the final product, the safety of the operation, and the overall energy efficiency of the process. Central to achieving such control are variable resistance heating elements, which convert electrical energy into heat. Among the various types of heating elements available, Silicon Carbide (SiC), Molybdenum Disilicide (MoSi2), and Nichrome stand out for their widespread use in industrial applications due to their reliability, efficiency, and capacity to operate at high temperatures.
However, the effectiveness of these heating elements does not solely depend on their material properties. Equally important is the manner in which power is controlled and delivered to these elements. The role of thyristor power controllers in managing the power supplied to heating elements cannot be overstated. These controllers offer a range of functionalities—including control feedback, current limiting, phase angle firing, and soft start capabilities—that are crucial for ensuring that the heating elements operate optimally, safely, and efficiently. This article explores the characteristics of SiC, MoSi2, and Nichrome heating elements, their industrial applications, and the importance of sophisticated power control techniques in their operation.
Types of Variable Resistance Heating Elements
Silicon Carbide (SiC) Elements
Silicon Carbide heating elements are highly regarded for their ability to function at extremely high temperatures. They can operate effectively at temperatures up to 1,600°C (2,912°F), making them suitable for demanding industrial applications such as metal heat treatment, glass production, and ceramic firing. One of the key advantages of SiC elements is their high thermal conductivity, which allows for efficient heat transfer, and their resistance to oxidation, which ensures longevity even in harsh environments.
However, SiC elements are not without their challenges. As these elements age, their electrical resistance increases, which can lead to inconsistent heating if not properly managed. This characteristic makes precise power control essential. Without it, the efficiency of the heating process could decline, leading to increased energy consumption and potential defects in the final product.
Molybdenum Disilicide (MoSi2) Elements
Molybdenum Disilicide heating elements are engineered for the highest temperature applications, with an operating range that can reach up to 1,800°C (3,272°F). These elements are integral to processes that require extreme heat, such as the production of advanced ceramics, glass, and specialty metals. MoSi2 elements are highly valued for their ability to maintain stability and efficiency at very high temperatures, as well as their resistance to oxidation at elevated temperatures, thanks to the formation of a protective silica (SiO2) layer on the element’s surface.
The electrical resistance of MoSi2 elements changes significantly with temperature, a characteristic that demands sophisticated power control mechanisms to ensure that these elements deliver consistent heat throughout their operational life. If not carefully controlled, the variability in resistance can lead to inefficiencies and potential overheating, which could compromise both the equipment and the safety of the operation.
Nichrome Wire
Nichrome, an alloy of nickel and chromium, is one of the most versatile heating elements used in industrial applications. It has an operating temperature of up to 1,200°C (2,192°F) and is commonly found in applications such as plastic extrusion, metal forming, and in various types of kilns and ovens. Nichrome is favored for its stability across a broad temperature range, its durability, and its ability to provide consistent heat output.
Nichrome’s resistance remains relatively stable over time, making it easier to control compared to SiC and MoSi2 elements. However, precision in power delivery is still crucial, especially in processes that require exact temperature control. Proper power management ensures that Nichrome elements operate efficiently, reduce energy waste, and maintain a long service life.
Importance of Power Control in Industrial Heating Applications
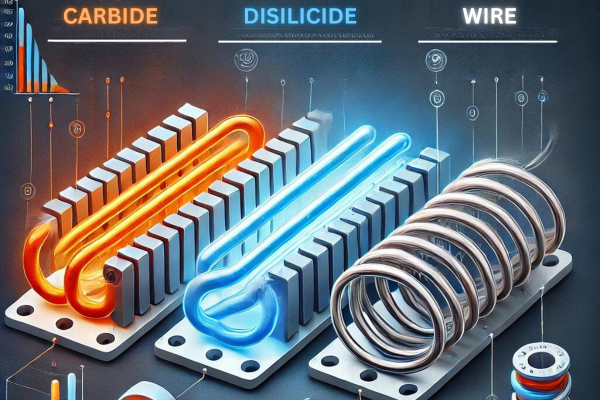
Effective power control is a cornerstone of successful industrial heating operations. It is essential for maximizing the efficiency of heating elements, ensuring product quality, enhancing safety, and minimizing energy consumption. Thyristor power controllers are the most common and effective devices used for managing the power supplied to heating elements. These controllers offer several advanced functionalities that are critical in industrial settings.
Control Feedback
Control feedback is a fundamental aspect of power control systems. In a feedback loop, the system continuously monitors the actual temperature of the heating element or the process being heated and compares it to the desired setpoint temperature. Any deviation from the setpoint triggers a corrective action, adjusting the power supplied to the heating element to bring the temperature back to the desired level.
For example, in a glass production furnace using Silicon Carbide heating elements, the temperature must be maintained within a very narrow range to ensure product quality. If the temperature starts to drift from the setpoint, the feedback system in the thyristor power controller will adjust the power input to the SiC elements to correct the temperature. This dynamic adjustment is crucial in maintaining process stability, preventing overheating, and avoiding energy waste.
Current Limiting
Current limiting is another essential feature of thyristor power controllers, particularly important for protecting both the heating elements and the power supply system. As heating elements, especially those like MoSi2, heat up, their resistance changes, which can lead to fluctuations in the current drawn by the element. Without current limiting, these fluctuations could cause the current to exceed safe levels, potentially damaging the heating elements or triggering a shutdown of the power supply system.
Thyristor power controllers equipped with current limiting functionality monitor the current flowing to the heating elements and automatically limit it to a predefined safe level. This ensures that the heating elements are not exposed to potentially damaging current spikes, thus extending their lifespan and maintaining the safety of the entire heating system.
Phase Angle Firing
Phase angle firing is a technique used by thyristor power controllers to regulate the power supplied to heating elements with high precision. In phase angle control, the power controller adjusts the point in the AC voltage cycle at which the thyristor is triggered to conduct current. By varying the trigger point, the controller can regulate the amount of power delivered to the heating element.
This method is particularly useful in applications that require very fine temperature control. For example, in a plastic extrusion process using Nichrome heating elements, phase angle firing can be used to ensure that the extruder barrel is heated to the exact temperature required for processing a specific type of plastic. By controlling the power delivered to the Nichrome element with high precision, the plastic can be heated uniformly, preventing defects and ensuring a high-quality final product.
Soft Start
Soft start functionality is designed to reduce the initial surge of current when a heating element is first powered on. When heating elements, particularly those made from materials like MoSi2, are cold, they have a lower resistance, which can lead to a large inrush of current when power is first applied. This inrush can cause excessive stress on the heating elements, reducing their lifespan and potentially damaging other components in the electrical system.
Thyristor power controllers with soft start capabilities gradually ramp up the power supplied to the heating elements, allowing them to warm up slowly and avoiding the inrush of current. This not only protects the heating elements but also improves the overall reliability and longevity of the heating system. In applications such as metal heat treatment, where MoSi2 elements are used, soft start functionality ensures that the elements are brought up to operating temperature smoothly, without the risk of sudden failures or interruptions.
Industrial Applications and Benefits of Advanced Power Control
The use of Silicon Carbide, Molybdenum Disilicide, and Nichrome heating elements spans a wide range of industrial applications, each with its own specific requirements for temperature control, efficiency, and safety. The integration of advanced power control techniques through thyristor power controllers enhances the performance of these heating elements in several ways:
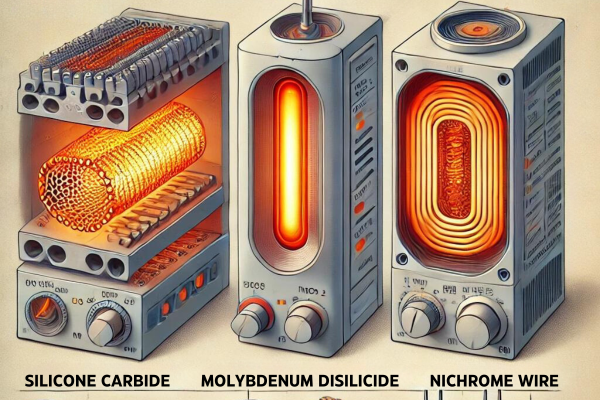
Energy Efficiency
One of the primary benefits of precise power control is improved energy efficiency. In industrial processes, energy costs can be significant, and any reduction in energy consumption can lead to substantial cost savings. By using control feedback and phase angle firing, thyristor power controllers can optimize the power delivered to heating elements, ensuring that only the necessary amount of energy is used to maintain the desired temperature. This reduces waste and lowers operational costs, which is particularly important in energy-intensive industries such as metal processing, glass manufacturing, and ceramics production.
Temperature Precision
In many industrial applications, maintaining precise temperature control is critical to achieving the desired product quality. For instance, in the production of specialty glass, even small deviations in temperature can lead to defects such as bubbles or cracks. By employing control feedback and phase angle firing, thyristor power controllers provide the level of precision needed to maintain consistent temperatures throughout the process. This results in higher quality products and reduces the need for rework or scrap, which further enhances efficiency and cost-effectiveness.
Safety
Safety is a paramount concern in industrial heating applications, where the potential for overheating, equipment failure, or electrical hazards is always present. The current limiting and soft start functionalities of thyristor power controllers play a crucial role in ensuring safe operation. By preventing current surges and controlling the power ramp-up, these features protect both the heating elements and the surrounding equipment from damage. This reduces the risk of accidents, equipment downtime, and costly repairs, contributing to a safer working environment.
Extended Lifespan of Heating Elements
Variable resistance heating elements, especially those like Silicon Carbide and Molybdenum Disilicide that operate at very high temperatures, are subject to significant thermal stress over time. By precisely controlling the power delivered to these elements, thyristor power controllers help to minimize this stress, thereby extending the operational lifespan of the heating elements. This not only reduces the frequency of element replacements but also enhances the overall reliability of the heating system. This leads to lower maintenance costs and improved uptime in industrial operations.
Conclusion
Silicon Carbide, Molybdenum Disilicide, and Nichrome heating elements are critical components in a wide range of industrial heating applications. Their ability to operate at high temperatures and their durability make them invaluable in processes such as metal heat treatment, glass production, and ceramics manufacturing. However, the effectiveness and longevity of these heating elements are highly dependent on the precision with which power is controlled.
Thyristor power controllers, with their advanced functionalities including control feedback, current limiting, phase angle firing, and soft start, are essential tools in managing the power supplied to these heating elements. These controllers ensure that the heating elements operate efficiently, safely, and within their optimal temperature ranges, which not only improves product quality but also reduces energy consumption and operational costs.
In conclusion, the integration of sophisticated power control techniques is crucial for maximizing the performance of variable resistance heating elements in industrial applications. As industries continue to seek ways to improve efficiency and reduce costs, the role of advanced power control will only become more important in ensuring the success of heating processes across various sectors.