Optimising Power in the Stretch Blow Moulding Process
For the efficiency and greater sustainability of the thermoplastics process, CD Automation has invested heavily to provide customers with customised power quality solutions.
Blow moulding is a plastics processing operation that produces a wide range of hollow-body items. Let’s dive into the stretch blow moulding process and explore the solutions offered by CD Automation in more detail.
Blowing is a simple and intuitive operation, but it involves several steps.
- The first step is to introduce the granule raw material into a heated cylinder.
- The plastic is then melted at high temperatures until it becomes pasty, before being extruded or injected via an extruder screw, to form a tubular plastic preform called the parison.
- The parison is clamped into a female mould containing the shape of the product to be produced.
- The plastic is inflated by blowing air into the preform, causing it to adhere to the walls of the mould.
- After the thermoplastic material has cooled and hardened, the mould opens, and the part is ejected.
The Blow Mould Process
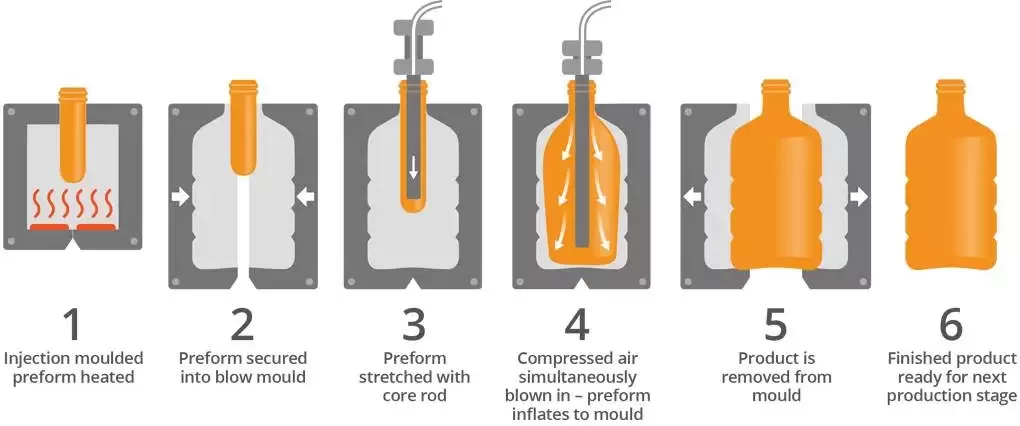
What are the advantages of this technology?
Blow moulding comes with a multitude of benefits, which include:
- shorter production times
- production of complex parts with adjustable weight and wall thickness
- handles can be integrated into packaging design, presenting new opportunities
This type of processing is also perfect for producing multi-layer packaging and containers that include a viewing window.
Focus on stretch-blow moulding
One of the many blow-moulding techniques used today is stretch-blow moulding. Commonly used in the beverage industry, stretch-blow moulding is used in the production of PET bottles. The process, used since the early 1970s, has spread widely due to the growing demand for carbonated beverage bottles.
The benefits
The ability to stretch the preform in a biaxial direction is one of the main advantages of stretch-blow moulding. Biaxial refers to the process that stretches the film over two directions, making it stronger and more transparent, resulting in a 10 to 15% reduction in the overall weight of the containers compared to other processes.
Extrusion Blow Moulding
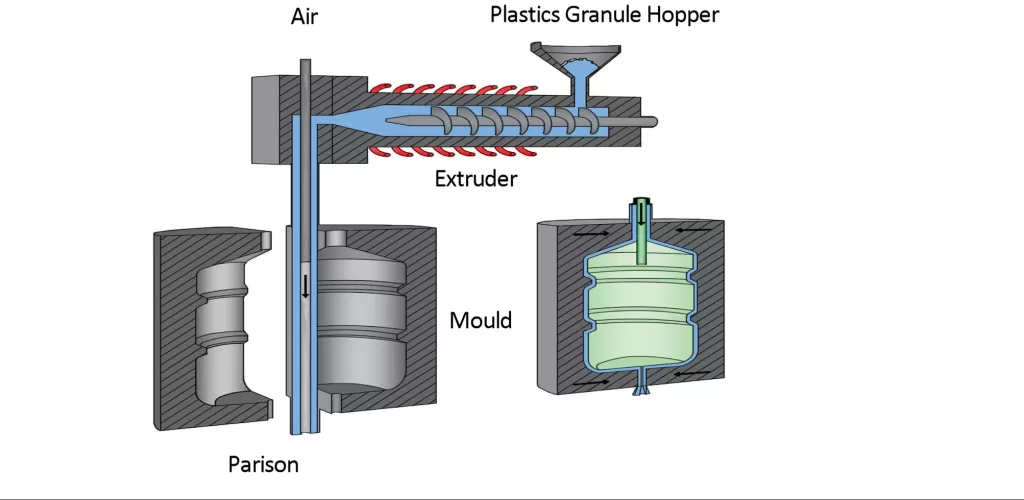
How to choose between single-stage or two-stage?
Stretch blow moulding can be split into single-stage and two-stage processes. The former uses the extruder to inject a preform into a mould, where the plastic is quickly cooled, resulting in the formation of the parison. Once it is softened, it can extend to approximately twice its original length. In the same machine, the operation then continues as described previously for blow moulding. This technique is effective in applications that do not need particularly high production speeds.
For high production volumes, two-stage stretch blow moulding is the preferred method. In contrast to the previous technique, previously manufactured preforms can be used allowing companies to produce or purchase their own preforms.
In this process, the injection machine moulds a preform, which is then transferred to another machine for blowing. Large production runs are usually necessary to justify the heavy expenditure on the injection and blow moulds required for two-stage stretch blow moulding needed to create the preform and obtain the container.
The separation of the injection mould process from the blow moulding process allows for optimization of both processes. This advantage allows for the storage, long-distance shipping, and on-demand use of preforms.
Two-stage application in the beverage sector
As part of the two-stage production process of Polyethylene Terephthalate (PET) bottles, stretch-blow moulding is essential, as it is the most widely used material in beverage packaging. The first stage of stretch blow moulding for this application involves injection moulding, where the machine produces parisons in the shape of a vial or test tube. While their neck sections are finished, the dimensions of the preforms are much smaller than those of the finished product, which is only obtained through the heated stretch-blow moulding phase.
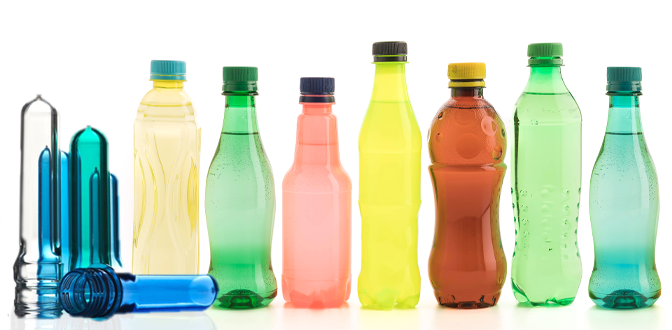
The CD Automation solution
With over 30 years of experience, CD Automation has developed REVO PN, a multi-channel thyristor power control unit that enhances the efficiency and sustainability of stretch blow moulding processes. With a small footprint, this unit is capable of handling applications with multiple power zones.
With REVO PN, the power distribution algorithm balances and limits the peak current demand, limiting power losses and reducing energy consumption.
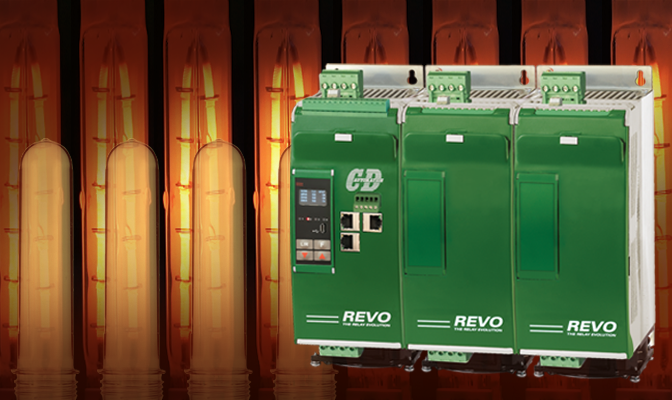
REVO PN Multizone Power Controller
The use of REVO PN in stretch blow moulding processes enables a significant reduction in power peaks, ensuring they remain below contractually agreed levels and preventing penalties and unexpected expenses.
A single unit has the capability of handling up to 24 short wave infrared heating lamps. To avoid voltage peaks and maintain a power factor close to 1, it is possible by synchronising the switching on of all channels. With the ability to communicate autonomously with the most common field buses, each module can diagnose heater element failures and short circuits on the thyristors at an early stage.
Last but not least, REVO PN’s ‘Dynamic burst firing’ mode reduces flickering in short-wave infrared lamp applications.
The Company
CD Automation’s range of thyristor power controllers, and a partner program of supporting products that includes temperature controllers, power line filters and network power meters, provides a complete solution to the thermal processing industry, delivering both exact heat regulation and accurate temperature and power reporting.
The REVO family of SCR power controllers meet the toughest design challenges and provide efficient, reliable and precise control of electrical heating, which is essential in quality industrial thermal processes including infrared drying, glass manufacturing, industrial furnaces, heat treatment, melting, drying and forming.
Our range of SCR power controllers offer unrivalled flexibility and performance, can help to improve product uniformity and quality, optimizes energy consumption, minimizes waste and probably, most importantly, machine breakdown.
Our products can be used as stand-alone units, connected to a bus system or used in combination with all PLCs, or computer systems.
Talk to our friendly support team today, we’d love to try and help improve your process, telephone 01323 811100 or email us here.